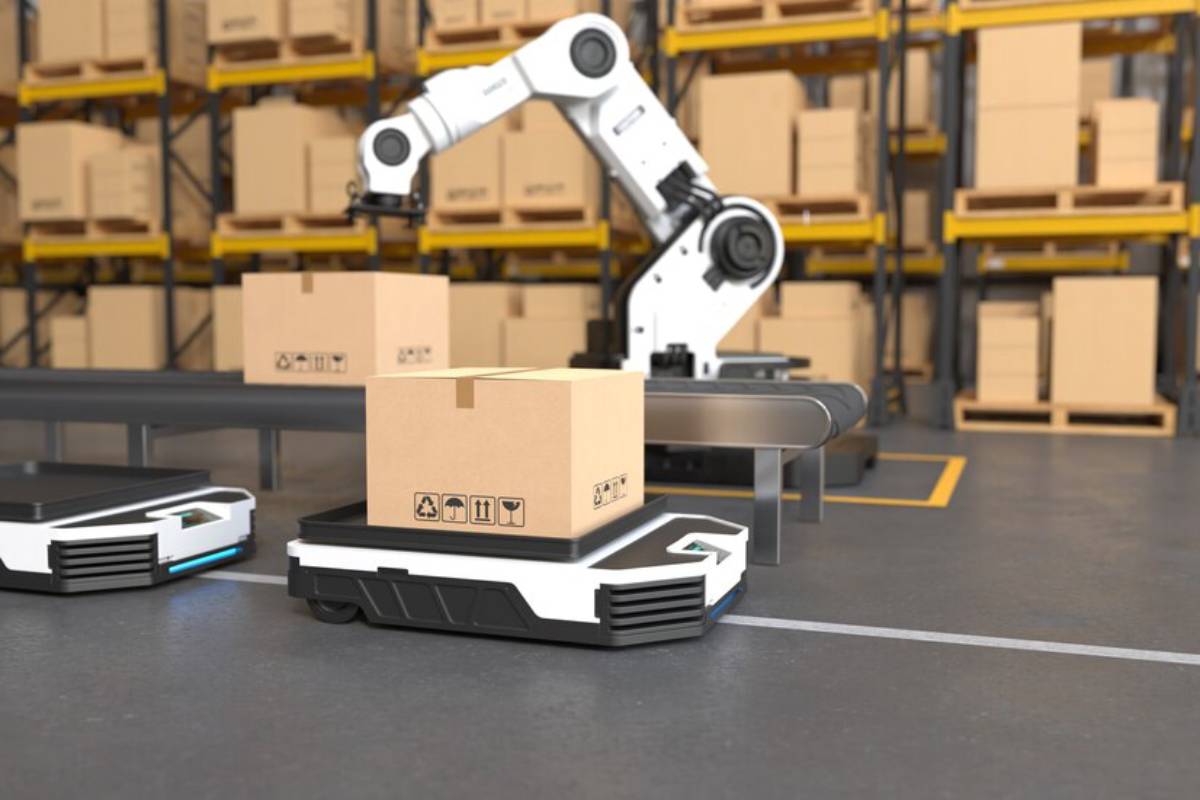
Automation in Warehousing: Robotics in Logistics
The global logistics industry is experiencing a technological renaissance. E-commerce is growing fast, and customers want quick, precise deliveries. This puts traditional warehousing methods under pressure. Warehouse automation has become a game-changer. It uses robotics, artificial intelligence, and smart infrastructure.
Logistics robots are now crucial. They include robotic arms that pick and pack items. They also have autonomous mobile vehicles that move around large storage areas. These innovations boost speed and accuracy. They also change what’s possible in today’s supply chain operations.
In this article, we look at the main technologies driving warehouse automation. We also explore how AI logistics is changing the industry. Finally, we assess the benefits and challenges of a robotic future in warehousing.
What Is Warehouse Automation?
Warehouse automation involves using technology to perform tasks traditionally carried out by humans—such as inventory tracking, picking, packing, and transporting goods. The goal is to streamline operations, reduce errors, and increase overall efficiency.
Automation can range from simple barcode scanning systems to advanced robotics and AI-driven warehouse management systems (WMS).
Key Technologies Include:
- Autonomous Mobile Robots (AMRs)
- Automated Guided Vehicles (AGVs)
- Robotic arms and pickers
- AI-powered analytics and optimisation tools
- Drones and machine vision systems
Together, these technologies create a fully integrated logistics environment that can adapt, scale, and respond to real-time demand.
The Role of Robotics in Logistics
1. Autonomous Mobile Robots (AMRs)
Unlike traditional AGVs that follow fixed paths, AMRs use sensors, cameras, and AI to map and navigate dynamic warehouse environments.
Use Cases:
- Transporting goods between picking and packing stations
- Replenishing stock on shelves
- Supporting humans in collaborative workflows
AMRs improve flexibility and reduce infrastructure costs, as they don’t require pre-set tracks or magnetic strips.
2. Robotic Picking Systems
These include robotic arms equipped with suction cups, grippers, and machine vision. They can:
- Identify and grasp items of varying shapes and sizes
- Sort products for delivery
- Operate continuously with minimal downtime
Thanks to advancements in AI and machine learning, these robots are becoming increasingly adept at handling fragile or irregular items—closing the gap between human and machine dexterity.
3. Conveyor and Sortation Systems
Automated conveyor belts and sortation systems help move and categorise goods quickly and accurately across the warehouse.
Features:
- High throughput
- Reduced manual handling
- Integration with AI for route optimisation
In high-volume distribution centres, such systems are essential for meeting tight shipping deadlines and reducing bottlenecks.
4. Drones for Inventory Management
Indoor drones are being used to scan barcodes and conduct inventory counts. Flying through aisles and capturing data, they can perform tasks that would otherwise take hours or days.
Advantages:
- Accurate and fast cycle counts
- Reduced need for cherry pickers or ladders
- Fewer interruptions to daily operations
Logistics robots like these are particularly beneficial in large or high-ceilinged warehouses.
AI Logistics: The Smart Backbone of Automation
AI is the engine that turns raw warehouse data into actionable insights. With AI, logistics systems are not just automated—they’re intelligent.
AI Applications in Warehousing:
- Demand forecasting to anticipate stock needs
- Route optimisation for internal and external transport
- Real-time decision-making in dynamic environments
- Predictive maintenance of machines and robotics
- Labour scheduling and productivity analysis
AI algorithms constantly learn from data, helping warehouses operate with maximum efficiency and minimum waste.
Benefits of Warehouse Automation and Robotics
1. Increased Productivity
Automated systems can operate 24/7 without fatigue, dramatically increasing throughput. Tasks that once took hours can now be completed in minutes.
2. Improved Accuracy
AI logistics systems reduce human error in picking, packing, and inventory management—leading to fewer returns and happier customers.
3. Cost Efficiency
Upfront investment is high, but automation cuts long-term costs. It helps save on labour, training, and fixing errors.
4. Scalability
Automated systems can quickly adjust to handle seasonal spikes or business growth. This provides more agility in a changing market.
5. Enhanced Worker Safety
Robots take over dangerous or repetitive tasks. This cuts down on workplace injuries and lets human workers focus on more important jobs.
Challenges and Considerations
Despite its many advantages, warehouse automation is not without challenges.
1. High Initial Investment
Robots and automation infrastructure can be expensive, particularly for small to mid-sized operations. ROI may take years to materialise without strategic planning.
2. Integration Complexity
New systems must be compatible with existing software, hardware, and workflows. A lack of interoperability can hinder performance.
3. Workforce Displacement
There’s growing concern that automation may lead to job losses in the logistics sector. It also creates new jobs in robot maintenance, systems management, and data analysis.
4. Cybersecurity Risks
With increased connectivity comes greater vulnerability. Protecting data and systems from cyberattacks is crucial.
Case Studies: Leaders in Robotic Warehousing
Amazon Robotics
Amazon’s fulfilment centres have thousands of robots that move goods to human pickers. Their system speeds things up and cuts labour costs. This lets them provide next-day and same-day delivery.
Ocado (UK)
The British online supermarket uses AI and robots to manage one of the world’s most advanced automated warehouses. Their bots quickly navigate a grid to collect groceries. They work efficiently and need little human help.
JD.com (China)
The Chinese e-commerce giant has automated warehouses. Robots handle almost every task, from sorting to packaging.
These examples show how logistics robots can change operations on a large scale. They offer insights for businesses of all sizes.
The Future of AI Logistics
As technology matures, the next phase of AI logistics will focus on:
- Interoperability: Seamless integration between robotic systems and cloud-based platforms.
- Collaborative robots (cobots): Machines designed to work safely and effectively alongside humans.
- Digital twins: Virtual models of physical warehouses used to simulate scenarios and optimise layouts.
- Green automation: Robotics that prioritise energy efficiency and reduce environmental impact.
In future warehouses, AI won’t just react to demand. It will also predict it. This means it can optimise stock levels, workforce needs, and delivery routes instantly.
Getting Started with Warehouse Automation
Thinking of integrating automation into your logistics operations? Here’s a step-by-step guide:
1. Assess Your Needs
Identify bottlenecks or repetitive tasks that could benefit from automation.
2. Start Small
Try out a project in a specific area of your warehouse, such as automated picking or inventory tracking, before you scale up.
3. Choose the Right Technology
Ensure compatibility with your current systems and long-term goals. Consider factors like ease of use, vendor support, and upgrade paths.
4. Train Your Team
Automation doesn’t eliminate the need for people. Invest in training to help staff adapt to new tools and roles.
5. Monitor and Refine
Track ROI with performance metrics. This helps you make smart choices about expanding or adjusting.
The Robotic Future Is Here
Warehouse automation is no longer new. It’s now a vital strategy for staying competitive in logistics. Logistics robots are changing the game. They power fulfilment centres and drive inventory systems. This integration boosts speed, efficiency, and intelligence.
The best warehouses will mix automation with human insight. They will mix data with action and link innovation to responsibility as the sector grows.
Act now: Begin a pilot automation project, speak with a robotics provider, or invest. The warehouses of the future are here. They are already picking, packing, and delivering with precision.